1. |
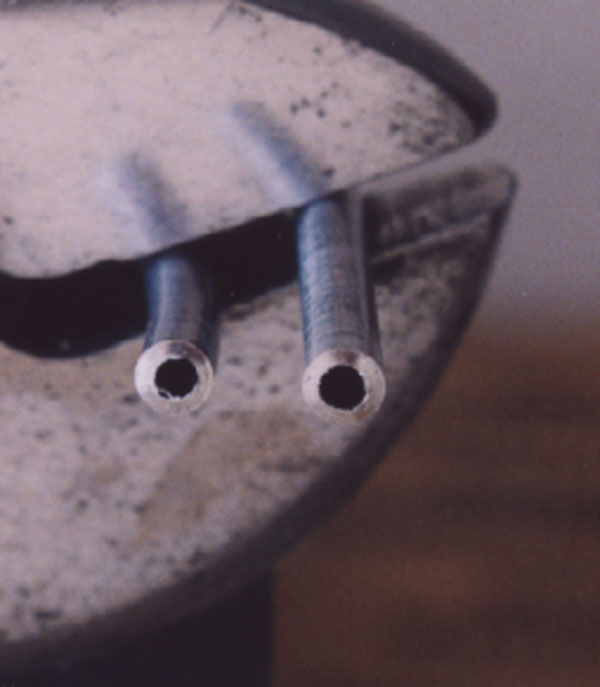 |
Cut the tubing to desired length. Make sure the cut is square to
the length of the tubing. I used a mini tubing cutter. You will
notice that the tubing openings are collapsed a little after the
cut is made.
|
2. |
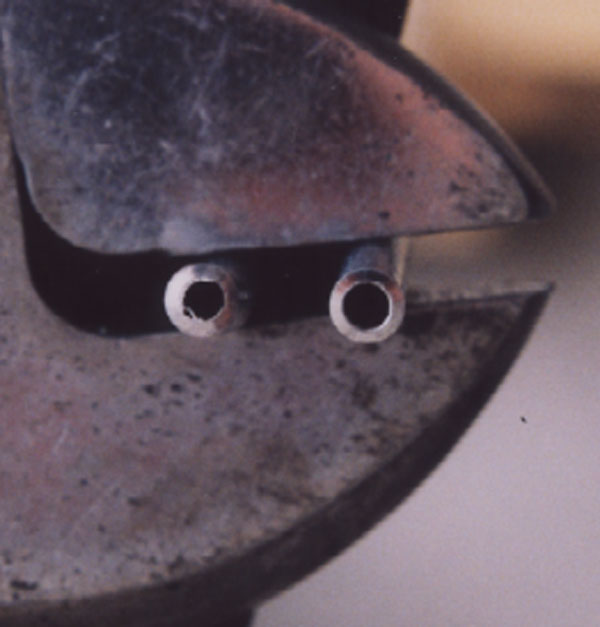 |
Take a 7/32 inch drill bit and put the point into the tubing opening
and turn by hand to deburr. You can compare the size of the opening
before (on left) and after (on right) this deburring process.
A 7/64 inch drill bit will slide into the tubing on the right and
a 1/8 in drill bit will not. The 7/64 inch drill bit will not fit
into the undeburred tubing end on the left.
|
3. |
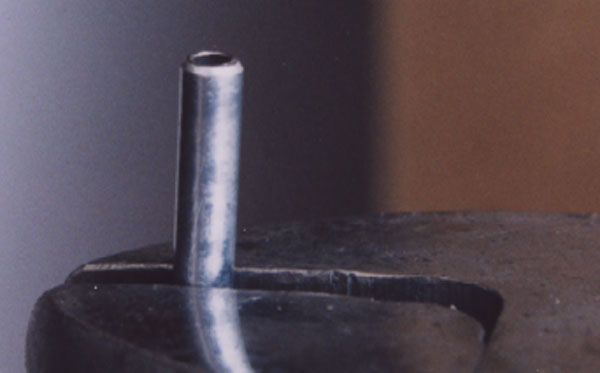 |
Now take a file (Craftsman 931265, 6 inch mill file) and chamfer
the edge of the tubing about 1/16th inch.
|
4. |
Put the Tubing Nut ON! PUT
THE TUBING NUT ON NOW!! |
Very Important to remember to put the tubing nut on now or you'll
have to cut off the beautiful flare you are about to make. |
5. |
 |
Insert the tubing into the flaring tool (Performance Tool
Double Flare Tool W80670 made by Wilmar Corp and purchased at Sears)
and adjust until the tubing
sticks out the proper length per your tools instructions. For my tool
the die is used as the guage so the tube just fits under the edge
of the inverted die. Tighten the tool to hold the tubing.
Make sure, as you continue the steps, that the tubing does not
slip in the tool. I had a tool from another manufacturer
that would not hold the tubing tight enough. After struggling with
it I found the Performance Tool and threw away the other brand.
I put a little grease on the tip of the tubing and on the
flaring tool anvil. Now invert the die and put the pin into the
tubing end and attach the anvil. Compress the tubing until the die
makes contact with the tool clamp.
|
6. |
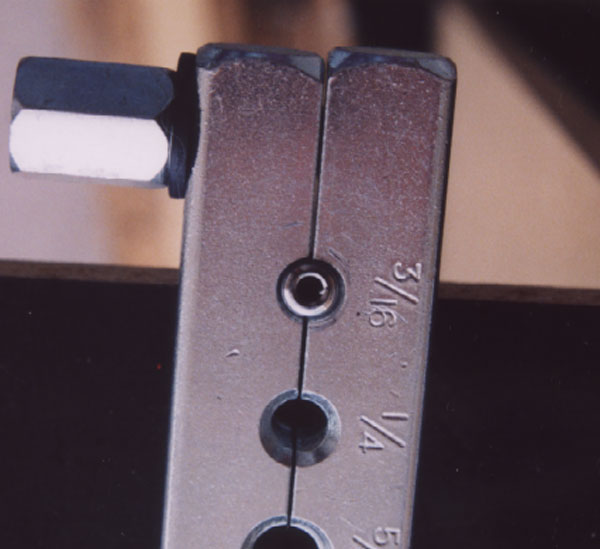 |
After removing the anvil and the die from the tubing this picture
shows what the tubing looks like after the above step. Essentially
it is a bubble flare.
|
7. |
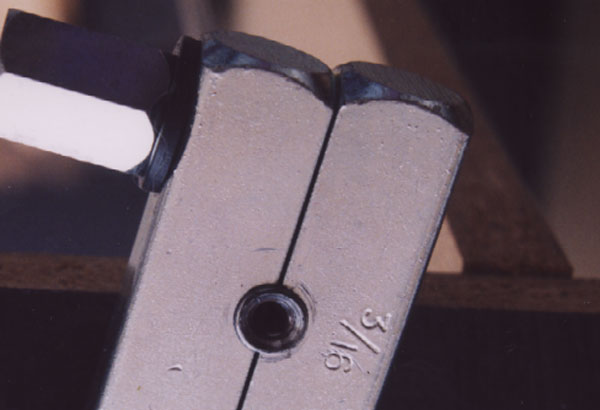 |
Complete the double flare by placing the tool anvil in the
center of the tubing and turn the press until tight. After
removing the anvil this is what the
completed double flare looks like in the tool clamp.
|
8. |
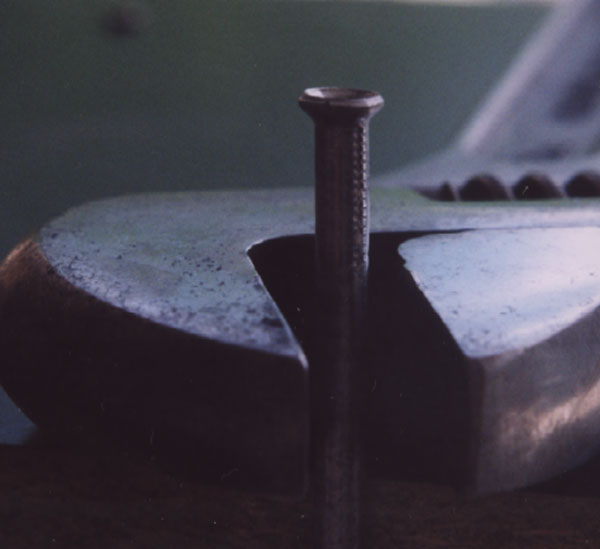 |
With practice the flare you make should look just as good as
one on the end of brake tubing purchased at your local parts store.
Mine |
|
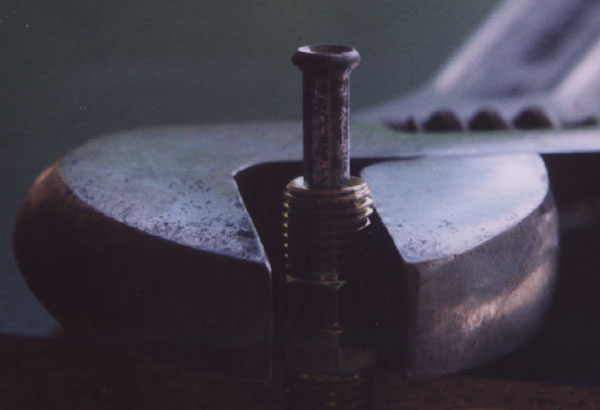 |
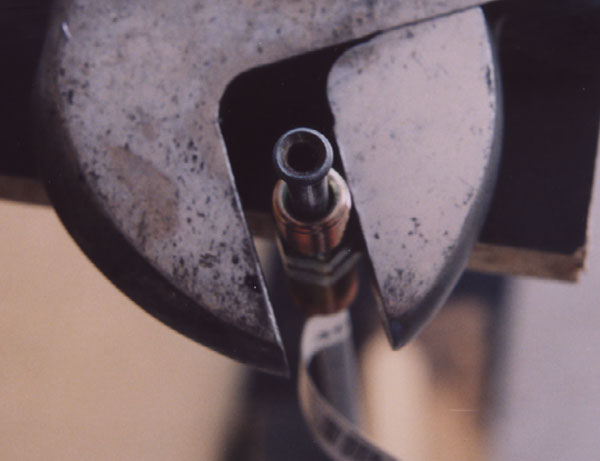
Commercial |
|